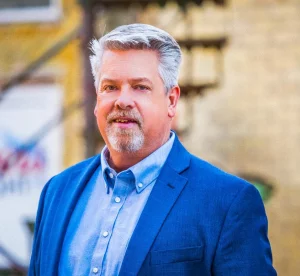
Bill Elmquist
President
Bill Elmquist')>
30 year focus on magnesium surface protection. Our firm developed the Tagnite coating process for magnesium, widely recognized as the most corrosion resistant coating available for magnesium alloys. Each day I work with our team as we apply Tagnite and various paints to magnesium components found on most every major aerospace and defense platform that uses magnesium. We are experts in processing large magnesium sand castings such as helicopter transmission housings and jet engine gearboxes. We also are the leaders in the field of coatings application for optical and UAS components made out of magnesium including gimbal ball cameras and optical benches.
Grand Forks, United States
Aerospace
About
Technology Applications Group, Inc. (TAG) developed the Tagnite coating for a simple reason: existing magnesium coatings were inadequate for the demanding environments in which the metal was being used. They lacked inherent corrosion resistance and, due to the chemicals employed, were environmentally hazardous.
The major property absent in the other magnesium coatings is corrosion resistance. Prior to the development of Tagnite, Chrome Manganese and Dow 7 provided almost no measurable corrosion resistance. Studies had ranked HAE and Dow 17, Chrome Manganese and Dow 7 as providing the best corrosion resistance. However, HAE and Dow 17 provided only a limited number of hours corrosion resistance protection when exposed to salt spray (ASTM B117 5%).
Environmental concerns were another key issue with other magnesium coatings. Most magnesium coatings (Dow 17, Dow 7, and Chrome Manganese) contain Chromium (VI), a carcinogen that is a major health hazard. At the time these coatings were developed, the health risks associated with Chromium (VI) were unknown.
With these issues to address, TAG set out to develop a coating which would provide superior corrosion resistance and be environmentally acceptable. The Tagnite coating has unmatched abrasion resistance and unequaled coating uniformity and is an excellent base for paint. We are proud of our coating technology and pleased to say it is being used by major aerospace companies.
The major property absent in the other magnesium coatings is corrosion resistance. Prior to the development of Tagnite, Chrome Manganese and Dow 7 provided almost no measurable corrosion resistance. Studies had ranked HAE and Dow 17, Chrome Manganese and Dow 7 as providing the best corrosion resistance. However, HAE and Dow 17 provided only a limited number of hours corrosion resistance protection when exposed to salt spray (ASTM B117 5%).
Environmental concerns were another key issue with other magnesium coatings. Most magnesium coatings (Dow 17, Dow 7, and Chrome Manganese) contain Chromium (VI), a carcinogen that is a major health hazard. At the time these coatings were developed, the health risks associated with Chromium (VI) were unknown.
With these issues to address, TAG set out to develop a coating which would provide superior corrosion resistance and be environmentally acceptable. The Tagnite coating has unmatched abrasion resistance and unequaled coating uniformity and is an excellent base for paint. We are proud of our coating technology and pleased to say it is being used by major aerospace companies.

Share
Recent Chats
Share via email
Future: handle WhatsApp here
Future: handle LinkedIn here
Future: handle Twitter here
SUBMENU HERE
Share via Chat
Copy Link